Tuesday, December 29, 2009
Cheap aircraft
I have read this report before, but it still remains quite interesting, it is about the FMX-4 Facetmobile: http://www.wainfan.com/pavreport.pdf
Tuesday, December 8, 2009
SpaceShipTwo unveiled
Here is a great article with pictures and video:
http://news.bbc.co.uk/2/hi/science/nature/8400353.stm
Awesomely pretty machine. I would like to fly that thing (as a pilot rather than passenger).
http://news.bbc.co.uk/2/hi/science/nature/8400353.stm
Awesomely pretty machine. I would like to fly that thing (as a pilot rather than passenger).
Sunday, December 6, 2009
MIT course materials online
I found this site quite interesting:
http://ocw.mit.edu/OcwWeb/web/courses/courses/index.htm#AeronauticsandAstronautics
MIT course lecture material online for everybody for free.
http://ocw.mit.edu/OcwWeb/web/courses/courses/index.htm#AeronauticsandAstronautics
MIT course lecture material online for everybody for free.
Sunday, November 15, 2009
PRELIMINARY AERODYNAMIC DESIGN CONSIDERATIONS FOR ADVANCED LAMINAR FLOW AIRCRAFT CONFIGURATIONS
NASA TP PRELIMINARY AERODYNAMIC DESIGN CONSIDERATIONS FOR ADVANCED LAMINAR FLOW AIRCRAFT CONFIGURATIONS can be found from the following link. I found it quite interesting.
http://ntrs.nasa.gov/archive/nasa/casi.ntrs.nasa.gov/19880014362_1988014362.pdf
http://ntrs.nasa.gov/archive/nasa/casi.ntrs.nasa.gov/19880014362_1988014362.pdf
Monday, October 26, 2009
KS118
You was able to see the polar of KS118 on the previous blog post. Here is the airfoil in question, it is very similar but slightly different from KS125.

KS118.DAT
Here is a wing simulation with this airfoil:
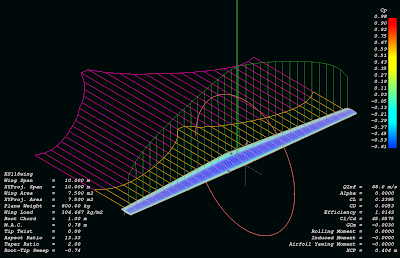
Comparison between NACA and KS118, 2D-simulation
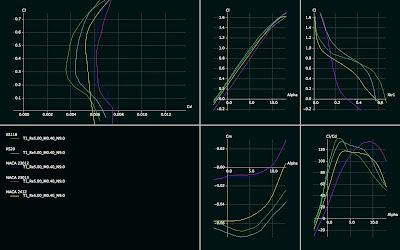
KS118 Cl-alpha polar, including stall region at 1M, comparison with NACA23012 and 23015 included:

KS118.DAT
Here is a wing simulation with this airfoil:
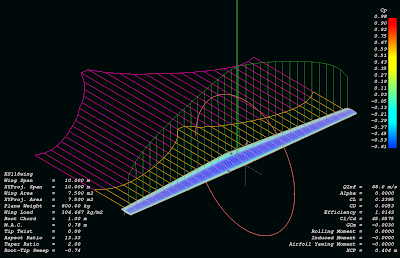
Comparison between NACA and KS118, 2D-simulation
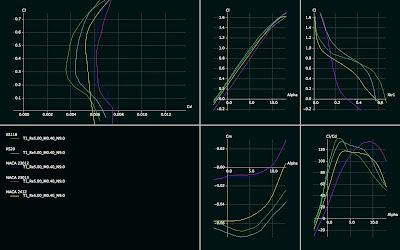
KS118 Cl-alpha polar, including stall region at 1M, comparison with NACA23012 and 23015 included:
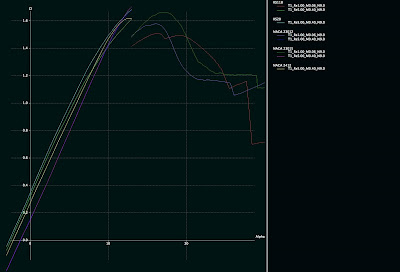
Saturday, October 24, 2009
Airfoil investigation database
Pretty neat airfoil database with search and quick illustration capabilities.
http://www.worldofkrauss.com/
http://www.worldofkrauss.com/
Friday, October 23, 2009
How to simulate a wing with QFLR5 -tutorial
1. Batch simulate airfoil for different Reynolds numbers so that the whole range of the wing is covered (speed you want to simulate + chord length on the root and tip). Fast way to calculate Reynolds numbers and mach numbers for your simulation case is to use this web page:
http://aero.stanford.edu/StdAtm.html
Use the metric values.
2. When you know your Mach number and Reynolds number range (ranging from tip to root), simulate the airfoil of your choice on QFLR5 on that range. Using batch analysis feature.
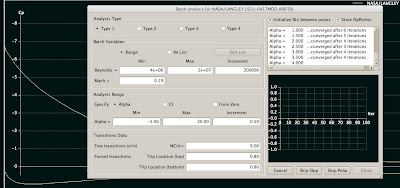
Please note that it can take significant amount of time to batch analysis all the airfoils you want to simulate (e.g. if your wing is going to use more than one airfoil for example, and if you want to compare it to other wings which have different airfoils).
3. Go to Wing and Plane Design. Select from Unit preferences. Replace millimeter units with meter, so you want m/s, m^2, m for length etc.
4. Select Define wing from the menu. A window with a spreadsheet appears.
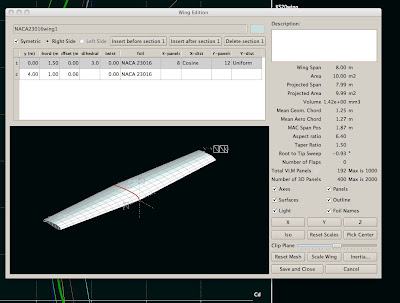
5. Define the wing by entering the y positions (you can define as many as you like). For simple taper it is enough to enter root to y position 0 and then tip to the position where the wing ends. For 12 meters long wing this position is 6 meters (as the plane is quite often symmetric). Select chord length for the root and tip. Select dihedral and twist for the root and tip. Select foil for the root and tip. Select the number of panels you want for the simulation. The more panels, the more accurate. Please note that the dimensions here affect to the Reynolds number, so if your simulation later says it is out of flight envelope, it means that you have not simulated in the Foil direct analysis section the appropriate Reynolds number range, something is missing. Please go back to the web site stated above and check your Reynolds numbers.
6. When you have a wing with desired shape with desired airfoils, click Save and Close from the bottom.
8. Select from Polars menu Define analysis. Select your simulation speed. Please note that this affects your Reynolds number. You need to know at this point your desired speed you want to fly. Select plane weight and moment location on the wing. You can
then select 3D panels. For example I have 150 kt, 800 kg, 0.40 m, 0.00, 0.00.
9. Analysis settings on the right, uncheck sequence if you are interested in one angle of attack only. This most likely is the case if you want to simulate a constant speed (e.g. the 150 kts described above). Then click Analyze and your wing is analyzed for that angle of attack.
Some examples of analyzed wings:
NACA4415:
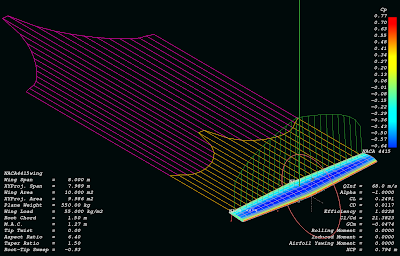
KS20 (same wing):
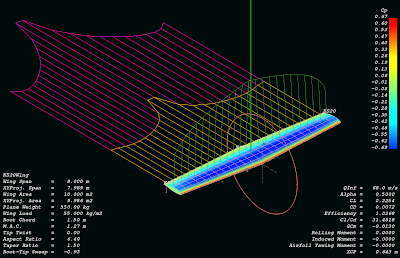
NASA NLF414F (same wing again):
http://aero.stanford.edu/StdAtm.html
Use the metric values.
2. When you know your Mach number and Reynolds number range (ranging from tip to root), simulate the airfoil of your choice on QFLR5 on that range. Using batch analysis feature.
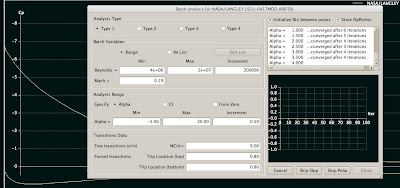
Please note that it can take significant amount of time to batch analysis all the airfoils you want to simulate (e.g. if your wing is going to use more than one airfoil for example, and if you want to compare it to other wings which have different airfoils).
3. Go to Wing and Plane Design. Select from Unit preferences. Replace millimeter units with meter, so you want m/s, m^2, m for length etc.
4. Select Define wing from the menu. A window with a spreadsheet appears.
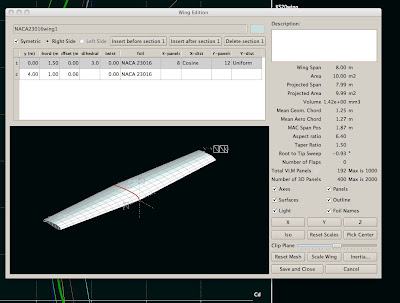
5. Define the wing by entering the y positions (you can define as many as you like). For simple taper it is enough to enter root to y position 0 and then tip to the position where the wing ends. For 12 meters long wing this position is 6 meters (as the plane is quite often symmetric). Select chord length for the root and tip. Select dihedral and twist for the root and tip. Select foil for the root and tip. Select the number of panels you want for the simulation. The more panels, the more accurate. Please note that the dimensions here affect to the Reynolds number, so if your simulation later says it is out of flight envelope, it means that you have not simulated in the Foil direct analysis section the appropriate Reynolds number range, something is missing. Please go back to the web site stated above and check your Reynolds numbers.
6. When you have a wing with desired shape with desired airfoils, click Save and Close from the bottom.
8. Select from Polars menu Define analysis. Select your simulation speed. Please note that this affects your Reynolds number. You need to know at this point your desired speed you want to fly. Select plane weight and moment location on the wing. You can
then select 3D panels. For example I have 150 kt, 800 kg, 0.40 m, 0.00, 0.00.
9. Analysis settings on the right, uncheck sequence if you are interested in one angle of attack only. This most likely is the case if you want to simulate a constant speed (e.g. the 150 kts described above). Then click Analyze and your wing is analyzed for that angle of attack.
Some examples of analyzed wings:
NACA4415:
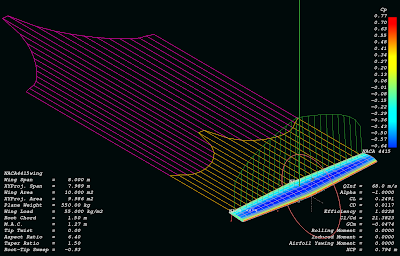
KS20 (same wing):
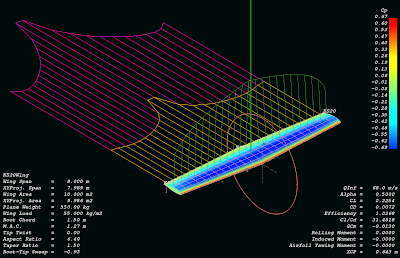
NASA NLF414F (same wing again):
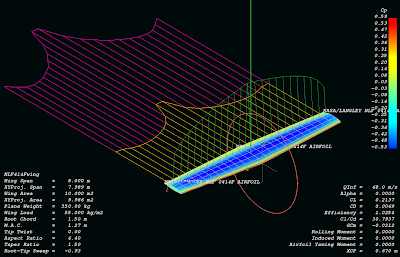
Monday, October 19, 2009
Monday, October 5, 2009
KSNLF51 airfoil - high L/D, high lift, low to medium Re
I created this airfoil one day. I was looking for getting high L/D at low Re. This is pretty nice. I tried simulations as low as Re 100000-300000 (not included in here, you can try by yourself with QFLR5).
Airfoil KSNLF51:

KSNLF51 L/D graph:
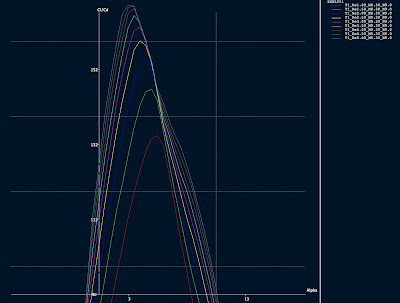
Data file: http://www.katix.org/karoliina/airfoils/KSNLF51.DAT
Polars:
Re 1 million, Mach 0.3
http://www.katix.org/karoliina/airfoils/KSNLF51_T1_Re1.00_M0.30_N9.0.txt
Re 3 millions, Mach 0.3
http://www.katix.org/karoliina/airfoils/KSNLF51_T1_Re3.00_M0.30_N9.0.txt
Re 5 millions, Mach 0.3
http://www.katix.org/karoliina/airfoils/KSNLF51_T1_Re5.00_M0.30_N9.0.txt
License: Creative Commons Share-a-like
Comparison between some airfoils:
Airfoil KSNLF51:

KSNLF51 L/D graph:
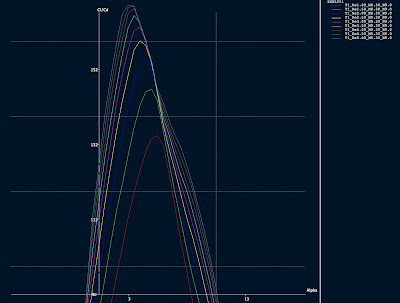
Data file: http://www.katix.org/karoliina/airfoils/KSNLF51.DAT
Polars:
Re 1 million, Mach 0.3
http://www.katix.org/karoliina/airfoils/KSNLF51_T1_Re1.00_M0.30_N9.0.txt
Re 3 millions, Mach 0.3
http://www.katix.org/karoliina/airfoils/KSNLF51_T1_Re3.00_M0.30_N9.0.txt
Re 5 millions, Mach 0.3
http://www.katix.org/karoliina/airfoils/KSNLF51_T1_Re5.00_M0.30_N9.0.txt
License: Creative Commons Share-a-like
Comparison between some airfoils:
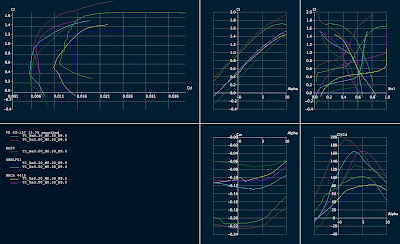
Monday, September 21, 2009
Sunday, September 6, 2009
Aerodynamic efficiency index, AEI
I have been trying to come up with my own formula (that differs from the various CAFE formulas to have a weighting that suits me better). I found another interesting comparative formula, the AEI.
AEI = (W0*U0)/hp
where W0 is the gross weight in lbs
where U0 is the free stream velocity in ft/s
where the hp is the horse power required
In other words for Diamond DA40 this is:
W0=1200 kg = 2640 lbs
U0= 214 ft/s (127 kts cruise at 10000 ft)
hp_cruise=90
=>
AEI(Diamond DA40) = (2640*214)/90
AEI(Diamond DA40) = 6277
Unlike the CAFE formula this has no weighting for these parameters.
If I would like to make my formula based on this, I might want to weight the hp a bit more.
That is because the lower the hp figure gets, the better is the fuel economy if everything else remains constant.
Why this index is good? Because it isolates aerodynamics from structural engineering and does not care how much useful load the craft has. It only considers the aerodynamically important point, how much power is required to move the mass forwards and at the same time keep it on air.
AEI = (W0*U0)/hp
where W0 is the gross weight in lbs
where U0 is the free stream velocity in ft/s
where the hp is the horse power required
In other words for Diamond DA40 this is:
W0=1200 kg = 2640 lbs
U0= 214 ft/s (127 kts cruise at 10000 ft)
hp_cruise=90
=>
AEI(Diamond DA40) = (2640*214)/90
AEI(Diamond DA40) = 6277
Unlike the CAFE formula this has no weighting for these parameters.
If I would like to make my formula based on this, I might want to weight the hp a bit more.
That is because the lower the hp figure gets, the better is the fuel economy if everything else remains constant.
Why this index is good? Because it isolates aerodynamics from structural engineering and does not care how much useful load the craft has. It only considers the aerodynamically important point, how much power is required to move the mass forwards and at the same time keep it on air.
Friday, September 4, 2009
AOPA article about Klaus Savier's 100 mpg Vari-Ez
Here is a link to the article by AOPA about Klaus Savier's Vari-Ez.
“For all these guys that think magnetos are so great, I only have one question: Why don’t you put magnetos in your cars?” Read more by clicking the link below:
http://www.aopa.org/aircraft/articles/2008/081230100mpg.html?WT.mc_id=090102epilot&WT.mc_sect=gan
“For all these guys that think magnetos are so great, I only have one question: Why don’t you put magnetos in your cars?” Read more by clicking the link below:
http://www.aopa.org/aircraft/articles/2008/081230100mpg.html?WT.mc_id=090102epilot&WT.mc_sect=gan
Thursday, September 3, 2009
Tuesday, September 1, 2009
TMS turbo installation on Rotax 914
Here is an article about turbo system of the highly modified Rotax:
http://www.designnews.com/article/13660-Turbo_power_reaches_new_heights.php
Interesting web site:
http://www.minijets.org/typo3/index.php
http://www.designnews.com/article/13660-Turbo_power_reaches_new_heights.php
Interesting web site:
http://www.minijets.org/typo3/index.php
Tuesday, August 25, 2009
Tractor vs. pusher
There is lots of strong feelings about tractor vs. pusher propeller configuration but no exact generic answer. Here is one article about the topic. Does not make definitive answer, but gives some background for the topic:
http://www.flyingmag.com/technicalities/1582/pusher-pusher.html
Here is another article:
http://dic.academic.ru/dic.nsf/enwiki/514042
Forum discussion
Another forum discussion
http://www.aiaa.org/content.cfm?pageid=406&gTable=mtgpaper&gID=50663
Tractor (prop forward of laminar flow wing):
http://www.aiaa.org/content.cfm?pageid=406&gTable=Paper&gID=1248
http://www.flyingmag.com/technicalities/1582/pusher-pusher.html
Here is another article:
http://dic.academic.ru/dic.nsf/enwiki/514042
Forum discussion
Another forum discussion
http://www.aiaa.org/content.cfm?pageid=406&gTable=mtgpaper&gID=50663
Tractor (prop forward of laminar flow wing):
http://www.aiaa.org/content.cfm?pageid=406&gTable=Paper&gID=1248
Monday, August 24, 2009
Hypotenuse and catheti and how blending makes wetted area not larger but actually smaller!
Most aircraft have larger than necessary wetted area and not so optimal body shape. One could think without thinking in more detail that wetted area is saved by lofting the plane so that the engine cowling is part of the main fairing and then there is a minimum canopy added on top of that.
However, a little thinking further: which one is the shortest route always, hypotenuse or catheti? Unlike the first thing which comes to mind when looking at planes and saving wetted area, instead of having this complicated shape, actually having more volume and fairing everything in the single form actually produces not only easiest path to the airflow, but also it produces lowest possible wetted area. So making the fuselage larger by removing canopy and putting the cockpit inside the main shape decreases wetted area and drag instead of increasing it. The shallower angle for windows does not decrease the visibility - the visibility can remain still the same. The only problem comes from the optical quality of the windows - as you are looking them from angled direction, you are looking through more plexiglass than you otherwise would and it can degrade the visibility. However - the visibility directly forwards is usually not so good in single engine aircraft which have engine in the front and it is neither better on planes without engine on front since somehow designers seem to not think that people would like to see straight forward very well too. Some twin engine planes have very high panels and poor visibility forwards despite of the fact not having the engine in front would make it possible to make the forward visibility a lot better than that.
So the design on CAD system becomes easy when the shape is not complicated but super simple. And in turn the super simple shape (convex to all directions though, in that sense not so simple, but I mean it is a single loft) has the best drag coefficient and the best wetted area too. At times it feels unbelievable that the solution can be so simple (and I have difficulty to believe it myself when looking e.g. our shared ownership Diamond DA40, it has many shapes, parts and forms), but who says that it has to have so many shapes. Nobody. So it will not have so many different shapes and forms if one shape can do it all. And who says the instrument panel needs to be panel and everything laid out to the panel? Nobody again. A bit more creativity and a lot better forward visibility is achieved despite of not having a bubble canopy and despite of having a pressurized fuselage.
Blending the fuselage to the wings increases frontal area. But who cares about the frontal area. It has very little effect to the drag in airplanes. It is all about wetted area and saving in the wetted area (in addition to maximizing the laminar flow). So blending the wing decreases wetted area - hypotenuse again, it is not a good idea to follow catheti. And the air likes that too - in fuselage wing joint the airflow can not sustain laminar flow. But what if you eliminate the joint and at the same time save in the wetted area. Great stuff.
One could say that it is hard to make a door to a such fuselage. Yes it is hard to make a door. But the solution for the door is to eliminate the door. A hatch that has no hinges and that is larger than the hole is the most light weight door one can imagine. It does not require complicated mechanism to hold it on place and it does not require lots of latches. It holds on place by itself because of the air pressure differential. It can be locked with a lot lesser heavy duty mechanics from inside to the fuselage. And how to ensure the hatch does not ever get out of the hole? That is super easy too: the hole and hatch can be circular and there is no way to put a larger circle out of a smaller circular hole. Not even magicians can do that!
Now then the window problem:
- to glue windows on pressurized fuselage, how to make sure the windows don't rip themselves out - how to glue them on place. Keep it simple and stupid solution: glue them to the inside so that they are larger than the hole in the fuselage. Now what, we have a problem that there is a dent outside of the fuselage on the window area which is really bad for the airflow. No problem again, there can be a simple non-pressurized window that is glued to the outside and faired level with the fuselage around it. It is also a fail-safe: if the windows that are exposed to outside get scratches, no problem, it does not affect the pressurized fuselage - these windows can be replaced fairly easily. And guess what, no bolts are needed, no rivets are needed, very simple.
Then how to get the blended fuselage to work with pressurization. Again super simple: the blend can be fairing on the outside and the pressure vessel can be tubular with completely circular cross section inside.
However, a little thinking further: which one is the shortest route always, hypotenuse or catheti? Unlike the first thing which comes to mind when looking at planes and saving wetted area, instead of having this complicated shape, actually having more volume and fairing everything in the single form actually produces not only easiest path to the airflow, but also it produces lowest possible wetted area. So making the fuselage larger by removing canopy and putting the cockpit inside the main shape decreases wetted area and drag instead of increasing it. The shallower angle for windows does not decrease the visibility - the visibility can remain still the same. The only problem comes from the optical quality of the windows - as you are looking them from angled direction, you are looking through more plexiglass than you otherwise would and it can degrade the visibility. However - the visibility directly forwards is usually not so good in single engine aircraft which have engine in the front and it is neither better on planes without engine on front since somehow designers seem to not think that people would like to see straight forward very well too. Some twin engine planes have very high panels and poor visibility forwards despite of the fact not having the engine in front would make it possible to make the forward visibility a lot better than that.
So the design on CAD system becomes easy when the shape is not complicated but super simple. And in turn the super simple shape (convex to all directions though, in that sense not so simple, but I mean it is a single loft) has the best drag coefficient and the best wetted area too. At times it feels unbelievable that the solution can be so simple (and I have difficulty to believe it myself when looking e.g. our shared ownership Diamond DA40, it has many shapes, parts and forms), but who says that it has to have so many shapes. Nobody. So it will not have so many different shapes and forms if one shape can do it all. And who says the instrument panel needs to be panel and everything laid out to the panel? Nobody again. A bit more creativity and a lot better forward visibility is achieved despite of not having a bubble canopy and despite of having a pressurized fuselage.
Blending the fuselage to the wings increases frontal area. But who cares about the frontal area. It has very little effect to the drag in airplanes. It is all about wetted area and saving in the wetted area (in addition to maximizing the laminar flow). So blending the wing decreases wetted area - hypotenuse again, it is not a good idea to follow catheti. And the air likes that too - in fuselage wing joint the airflow can not sustain laminar flow. But what if you eliminate the joint and at the same time save in the wetted area. Great stuff.
One could say that it is hard to make a door to a such fuselage. Yes it is hard to make a door. But the solution for the door is to eliminate the door. A hatch that has no hinges and that is larger than the hole is the most light weight door one can imagine. It does not require complicated mechanism to hold it on place and it does not require lots of latches. It holds on place by itself because of the air pressure differential. It can be locked with a lot lesser heavy duty mechanics from inside to the fuselage. And how to ensure the hatch does not ever get out of the hole? That is super easy too: the hole and hatch can be circular and there is no way to put a larger circle out of a smaller circular hole. Not even magicians can do that!
Now then the window problem:
- to glue windows on pressurized fuselage, how to make sure the windows don't rip themselves out - how to glue them on place. Keep it simple and stupid solution: glue them to the inside so that they are larger than the hole in the fuselage. Now what, we have a problem that there is a dent outside of the fuselage on the window area which is really bad for the airflow. No problem again, there can be a simple non-pressurized window that is glued to the outside and faired level with the fuselage around it. It is also a fail-safe: if the windows that are exposed to outside get scratches, no problem, it does not affect the pressurized fuselage - these windows can be replaced fairly easily. And guess what, no bolts are needed, no rivets are needed, very simple.
Then how to get the blended fuselage to work with pressurization. Again super simple: the blend can be fairing on the outside and the pressure vessel can be tubular with completely circular cross section inside.
Saturday, August 22, 2009
First atlantic crossing completed
We completed the first atlantic crossing in the N756DS (Diamond DA40) on Wednesday and arrived to Helsinki-Malmi. There will be a presentation about the trip in SIL-luokka Helsinki-Malmi later. I will let you know more about it when I know more details and have prepared the presentation. If you are a reporter in a newspaper or magazine and want to write a story about our not so ordinary adventure, feel free to contact me karoliina dot t dot salminen at gmail dot com.
We received the ferry flight training from Edward Carlson.
We want to do the trip again also, if you are looking for inexpensive ferrying from USA to Finlandm or to any other European country via Denmark/Opmas, I am glad to inform that the Danish VAT will work still to next summer as followings: if you buy aircraft this year before the end of the year and complete all the agreements, according to Opmas, the plane can still benefit from the Danish VAT if it is ferried on the first half of 2010. We would be glad to help for free (no ferry flight fee) at the price of the expenses (gasoline, hotel (we choose cheapest options always), maintenance needed for the plane, airport fees). If you are interested in inexpensive ferry (or should I say delivery) flight, please contact me to the abovementioned address. You can not fly the North Atlantic for first time by yourself, but you need someone that has flown it before to get insurance (which is mandatory for the flight). We have now flown it once and are willing to help people who haven't flown it yet and/or who do not want to fly it by themselves. The summer time is the best time for ferrying an aircraft because of weather. We will spend our summer vacation for flying your plane for free, you can not get better deal from anybody. We agree to fly the following aircraft make and models: Diamond DA40-180/G1000, Diamond DA40XL/G1000, Diamond DA40-CS/G1000, Diamond DA40-180/Avidyne, Cirrus SR20/Avidyne, Cirrus SR22/Avidyne, Cirrus SR22/Garmin Perspective or Diamond or Cirrus with any other comparable glass cockpit avionics - this list is based on our prior flying experience - we have flown Diamonds and Cirruses before. We can consider also other aircraft, but that will rise the expenses a bit since we need to get checked out to these prior flying the trip. I could estimate that most familiar of those would be Columbia 350, Columbia 400, Cessna 350 Corvalis, Cessna 400 Corvalis and these we would be glad to fly providing that we would get proper check-out before starting the trip to feel comfortable enough flying the plane in not so ideal conditions. We may not agree to fly steam-gauge IFR planes and surely will not agree to fly VFR-only equipped planes. Also we will not fly C172, because that is not suitable for the trip. We are not interested in taking unnecessary risks, we want to deliver.
We received the ferry flight training from Edward Carlson.
We want to do the trip again also, if you are looking for inexpensive ferrying from USA to Finlandm or to any other European country via Denmark/Opmas, I am glad to inform that the Danish VAT will work still to next summer as followings: if you buy aircraft this year before the end of the year and complete all the agreements, according to Opmas, the plane can still benefit from the Danish VAT if it is ferried on the first half of 2010. We would be glad to help for free (no ferry flight fee) at the price of the expenses (gasoline, hotel (we choose cheapest options always), maintenance needed for the plane, airport fees). If you are interested in inexpensive ferry (or should I say delivery) flight, please contact me to the abovementioned address. You can not fly the North Atlantic for first time by yourself, but you need someone that has flown it before to get insurance (which is mandatory for the flight). We have now flown it once and are willing to help people who haven't flown it yet and/or who do not want to fly it by themselves. The summer time is the best time for ferrying an aircraft because of weather. We will spend our summer vacation for flying your plane for free, you can not get better deal from anybody. We agree to fly the following aircraft make and models: Diamond DA40-180/G1000, Diamond DA40XL/G1000, Diamond DA40-CS/G1000, Diamond DA40-180/Avidyne, Cirrus SR20/Avidyne, Cirrus SR22/Avidyne, Cirrus SR22/Garmin Perspective or Diamond or Cirrus with any other comparable glass cockpit avionics - this list is based on our prior flying experience - we have flown Diamonds and Cirruses before. We can consider also other aircraft, but that will rise the expenses a bit since we need to get checked out to these prior flying the trip. I could estimate that most familiar of those would be Columbia 350, Columbia 400, Cessna 350 Corvalis, Cessna 400 Corvalis and these we would be glad to fly providing that we would get proper check-out before starting the trip to feel comfortable enough flying the plane in not so ideal conditions. We may not agree to fly steam-gauge IFR planes and surely will not agree to fly VFR-only equipped planes. Also we will not fly C172, because that is not suitable for the trip. We are not interested in taking unnecessary risks, we want to deliver.
Sunday, August 16, 2009
First Northern Atlantic Crossing
I have been recently a bit silent on this blog. The reason have been that I have been too busy and out of Internet most of the time. In other words, I have been flying.
I am typing this from Iceland. Our trip has been so far quite incredible:
1. from Helsinki to Miami with airliner
2. from Miami to Jacksonville with car
3. from Jacksonville to St. Louis with plane, N756DS
4. from St. Louis to Pueblo with N756DS
5. from Pueblo to Palo Alto with N756DS
6. IFR training in San Francisco Bay Area with N756DS
7. from Palo Alto to Sioux Falls with N756DS
8. from Sioux Falls to Oshkosh with N756DS
9. spent couple of days in Oskosh/Airventure 2009. Camp with Cozygirrrls.
10. from Oshkosh to Rhode Island with N756DS
11. from Rhode Island to Wabush (Canada) with N756DS. First Northern Atlantic Crossing in a small airplane was started for us. We are flying with Ed Carlson (he is a ferry flight instructor specialized in Northern Atlantic crossing).
12. from Wabush to Kuujjaq (Canada) with N756DS
13. from Kuujjaq (Canada) to Iqaluit (Canada) with N756DS
14. from Iqaluit (Canada) to Kangerlussuaq (Greenland) with N756DS
15. from Kangerlussuaq (Greenland) to Kulusuk (Greenland) with N756DS
16. from Kulusuk (Greenland) to Reykjavik (Iceland) with N756DS
17. from Reykjavik (Iceland) to EGILSSTADIR with N756DS
We will continue to Faroe Island / Vagar next. After that is either Bergen or Stavanger in Norway.
Kate has been keeping a blog about the adventure here:
http://n756ds.blogspot.com
I am typing this from Iceland. Our trip has been so far quite incredible:
1. from Helsinki to Miami with airliner
2. from Miami to Jacksonville with car
3. from Jacksonville to St. Louis with plane, N756DS
4. from St. Louis to Pueblo with N756DS
5. from Pueblo to Palo Alto with N756DS
6. IFR training in San Francisco Bay Area with N756DS
7. from Palo Alto to Sioux Falls with N756DS
8. from Sioux Falls to Oshkosh with N756DS
9. spent couple of days in Oskosh/Airventure 2009. Camp with Cozygirrrls.
10. from Oshkosh to Rhode Island with N756DS
11. from Rhode Island to Wabush (Canada) with N756DS. First Northern Atlantic Crossing in a small airplane was started for us. We are flying with Ed Carlson (he is a ferry flight instructor specialized in Northern Atlantic crossing).
12. from Wabush to Kuujjaq (Canada) with N756DS
13. from Kuujjaq (Canada) to Iqaluit (Canada) with N756DS
14. from Iqaluit (Canada) to Kangerlussuaq (Greenland) with N756DS
15. from Kangerlussuaq (Greenland) to Kulusuk (Greenland) with N756DS
16. from Kulusuk (Greenland) to Reykjavik (Iceland) with N756DS
17. from Reykjavik (Iceland) to EGILSSTADIR with N756DS
We will continue to Faroe Island / Vagar next. After that is either Bergen or Stavanger in Norway.
Kate has been keeping a blog about the adventure here:
http://n756ds.blogspot.com
Sunday, June 28, 2009
Sunday, June 7, 2009
LINK: How to design blended wing body RC airplane
http://rcairplanedesign.googlepages.com/Design-BWB-Blended-Wing-Body-RCplane.htm
The mentioned AVL can be found from the following address:
http://web.mit.edu/drela/Public/web/avl/
The mentioned AVL can be found from the following address:
http://web.mit.edu/drela/Public/web/avl/
Thursday, June 4, 2009
Sunday, May 31, 2009
Misc tech paper etc. link collection
I created a wiki page to katix gforge for link collection.
I hope you like it. It is not sorted in any sense, but it contains lots of interesting links. A friend of mine has been sending these to me a quite long time and I thought that I could share the collection with you.
http://gforge.katix.org/gf/project/twinzygger/wiki/?pagename=MiscTechPapers
I hope you like it. It is not sorted in any sense, but it contains lots of interesting links. A friend of mine has been sending these to me a quite long time and I thought that I could share the collection with you.
http://gforge.katix.org/gf/project/twinzygger/wiki/?pagename=MiscTechPapers
Wednesday, May 27, 2009
Tailed blended wing body with laminar flow body and Goldschmied suction and pressure thrust
New idea:
- A body that comprises of a laminar body and wing blended together
- There is a V-tail in a blended boom
- Rear of the center section has suction slot on top side
- The boom contains a electric fan that is used for suction and additional thrust
- There are two turbocharged Rotax 912UL engines in the wings which are hidden in blended pods that continue the airfoil shape of the wing without interruption
- Both engines turn additional turbochargers which drive generators which generate electricity for the rear fan of the aircraft
Items that need to be studied:
- does pressure thrust work with this kind of shape, or does it require axisymmetric body?
- compare the drag of minimum axisymmetric body with non-blended wings to a blended wing body which has larger cross sectional area, but potentially lower wetted area.
- wing incidence relative to the center section - center section has a lower aspect ratio than the wings and what it requires to achieve optimal lift distribution in this combined case
- the achievable gain from the lack of interference drag or very small interference drag
- optimal wing loading for a combined blended wing body compared to a pod+boom+wings solution
- shark fin shape on the outer wing sections, the gain and the issues
- A body that comprises of a laminar body and wing blended together
- There is a V-tail in a blended boom
- Rear of the center section has suction slot on top side
- The boom contains a electric fan that is used for suction and additional thrust
- There are two turbocharged Rotax 912UL engines in the wings which are hidden in blended pods that continue the airfoil shape of the wing without interruption
- Both engines turn additional turbochargers which drive generators which generate electricity for the rear fan of the aircraft
Items that need to be studied:
- does pressure thrust work with this kind of shape, or does it require axisymmetric body?
- compare the drag of minimum axisymmetric body with non-blended wings to a blended wing body which has larger cross sectional area, but potentially lower wetted area.
- wing incidence relative to the center section - center section has a lower aspect ratio than the wings and what it requires to achieve optimal lift distribution in this combined case
- the achievable gain from the lack of interference drag or very small interference drag
- optimal wing loading for a combined blended wing body compared to a pod+boom+wings solution
- shark fin shape on the outer wing sections, the gain and the issues
Saturday, May 23, 2009
Thursday, May 21, 2009
High transition length NLF body
I was looking Parson's high transition length body in a book and thought that maybe if I modify my body shape also so that the nose becomes sharper. By sacrificing some interior space, the flow acceleration can be kept for high transition length according the book I was reading this. My modified body looks like this.

Despite the QFLR5 algorithm is not maybe designed for simulating NLF bodies (it is designed for simulating wings), the pressure distribution looks like the same as the wind tunnel data for the Parson's body which makes me think that it might not be that much wrong.

Despite the QFLR5 algorithm is not maybe designed for simulating NLF bodies (it is designed for simulating wings), the pressure distribution looks like the same as the wind tunnel data for the Parson's body which makes me think that it might not be that much wrong.
Wednesday, May 20, 2009
Wolfram
Ever wanted a Star Trek's computer? It is here today:
http://www.wolframalpha.com/
For starters, try out for example: integrate x+y^2
This service is superb.
http://www.wolframalpha.com/
For starters, try out for example: integrate x+y^2
This service is superb.
Thursday, May 14, 2009
Random thinking about the feasibility of fabrication of a partial pressure suit
I have been thinking this topic for quite a long time and my old conclusion was that it is not feasible. However, there is very little information about pressure suits out there, but looking at the very little there is about the old Mercury suits etc., I have got indications that actually fabrication of a partial pressure suit might be feasible. Buying one might not be feasible because of lack of availability and insane pricing.
I would like to learn more about the topic, but in the Internet at least, there is very little or nothing. If someone has some insight, please leave some comments.
I would like to learn more about the topic, but in the Internet at least, there is very little or nothing. If someone has some insight, please leave some comments.
Wednesday, May 13, 2009
Fuselage drag reduction principle

A major portion of aircraft drag (in addition to the wing) is generated by the fuselage. The poor aircraft has to drag the draggy fuselage forwards. It is justified to target for reducing the fuselage drag in addition to the drag of the wings to achieve high L/D ratio and thus high efficiency and exceptional miles per gallon figure.
The idea comprises of the following claims:
- a laminar body with optimal fineness ratio for minimum drag
- a tail boom behind the optimal fineness ratio laminar pod
- electric motor (or couple of electric motors in cascade) turn
one or many ducted fans that are in cascade inside the rear of the fuselage.
The fan(s) take their air intake from the boundary layer of the fuselage.
- the fans are driven with batteries on takeoff.
- the fans are driven in cruise with electricity generated from the exhaust gas of the two gasoline engines which are mounted in wings.
- there is an additional turbine mounted in the exhaust that turns a generator rather than compressing air for the gasoline engine.
- the exhaust for the air is either in the tail boom prior to the tail or after the tail, whichever is found to provide best results.
- the fans provide suction for the fuselage boundary layer and also additional thrust for the aircraft. This configuration however, does not cause additional drag for the aircraft but reduces it.
- additional generators can be mounted to wing tip vortices so that the wing tip vortex turns the turbine blades and thus generates electricity for the fans located in the rear of the fuselage.
- the generators, battery charging and fans are computer controlled.
- the fans utilize all power that can be drawn from the exhaust gas and the wing tip turbines and thus runs at full power available to it continuously. On takeoff batteries are used to ensure high centerline thrust for the hypothetical situation where one of the gasoline engines would fail.
Goldschmied papers online
I found these some time ago, but now got reminded about it also on one comment to a previous post. Therefore I decided to open a new topic for it:
Goldschmied drag reduction tech papers:
http://cafefoundation.org/v2/pav_enablingtech_dragreduction.php
Interesting reading for anyone interested in achieving major breakthroughs in the fuselage drag.
Goldschmied drag reduction tech papers:
http://cafefoundation.org/v2/pav_enablingtech_dragreduction.php
Interesting reading for anyone interested in achieving major breakthroughs in the fuselage drag.
Thursday, May 7, 2009
Looking at historical data
One interesting aircraft in the historical data:
Lancair Evolution
P/W Power to weight ratio 7.54 kg/kW, 12.28 lbs/hp.
W/S Wing loading 142 kg/m^2, 29.05 lbs/sqft
Stall speed 61 kts
Empty weight to gross weight ratio: 0.55
Fuel to gross weight ratio: 0.2
Aspect ratio: 10.3
Aircraft with 12.28 lbs/hp power loading and 29.05 lbs/sqft wing loading in other words can
be made to climb, and it can also meet FAR 23 in stall speed requirement (61 kts). According to an article, the LC Evolution demonstrated glide ratio of 1:22 which is amazing compared to the competition, especially achieving this with only AR=10.3.
With these parameters, a smaller Rotax powered twin aircraft would be sized as follows:
Engines: 2 x Rotax 912UL, each turbocharged at 100 hp
Gross weight: 1116 kg
Empty weight: 0.55 * 1116 kg = 613 kg
Fuel weight: 0.2 * 1116 kg = 223 kg
Fuel volume: 314 l
Wing area: 1116 kg / 142 kg/m2 = 7.75 m2
Useful load (including fuel): 503 kg
Useful load full fuel: 280 kg
Endurance: 10.4 hours
Challenges:
- achieving the stall speed of 61 kts, requires very high Clmax for the flapped airfoil
- achieving > 20 glide ratio with lower Re, requires higher AR most likely
- achieving positive climb rate with single engine
- achieve the Clmax with wings that carry two engine pods on them (blanketing potentially flap and part of the wing).
- The fuel potentially does not fit inside the wing of this low wing area.
What it shows:
- Still with this high wing loading, it would be possible to fit three adults on the plane with full fuel. The result is not at all bad compared to any production aircraft.
- Empty weight looks realistic taking in account there are two Rotax engines on the craft. It is higher than it would be if it was relatively as lightweight as a Dynaero.
Bottom line: The parameters of the Lancair Evolution are very impressive and inspiring.
Realism hits:
Reduce the wing loading to 120 kg/m2
Wing area becomes: 1116 kg / 120 kg/m2 = 9.3 m2
-> It ends up in the magic 9.3 m2 wing area I have ended up from many directions already several times before.
Lancair Evolution
P/W Power to weight ratio 7.54 kg/kW, 12.28 lbs/hp.
W/S Wing loading 142 kg/m^2, 29.05 lbs/sqft
Stall speed 61 kts
Empty weight to gross weight ratio: 0.55
Fuel to gross weight ratio: 0.2
Aspect ratio: 10.3
Aircraft with 12.28 lbs/hp power loading and 29.05 lbs/sqft wing loading in other words can
be made to climb, and it can also meet FAR 23 in stall speed requirement (61 kts). According to an article, the LC Evolution demonstrated glide ratio of 1:22 which is amazing compared to the competition, especially achieving this with only AR=10.3.
With these parameters, a smaller Rotax powered twin aircraft would be sized as follows:
Engines: 2 x Rotax 912UL, each turbocharged at 100 hp
Gross weight: 1116 kg
Empty weight: 0.55 * 1116 kg = 613 kg
Fuel weight: 0.2 * 1116 kg = 223 kg
Fuel volume: 314 l
Wing area: 1116 kg / 142 kg/m2 = 7.75 m2
Useful load (including fuel): 503 kg
Useful load full fuel: 280 kg
Endurance: 10.4 hours
Challenges:
- achieving the stall speed of 61 kts, requires very high Clmax for the flapped airfoil
- achieving > 20 glide ratio with lower Re, requires higher AR most likely
- achieving positive climb rate with single engine
- achieve the Clmax with wings that carry two engine pods on them (blanketing potentially flap and part of the wing).
- The fuel potentially does not fit inside the wing of this low wing area.
What it shows:
- Still with this high wing loading, it would be possible to fit three adults on the plane with full fuel. The result is not at all bad compared to any production aircraft.
- Empty weight looks realistic taking in account there are two Rotax engines on the craft. It is higher than it would be if it was relatively as lightweight as a Dynaero.
Bottom line: The parameters of the Lancair Evolution are very impressive and inspiring.
Realism hits:
Reduce the wing loading to 120 kg/m2
Wing area becomes: 1116 kg / 120 kg/m2 = 9.3 m2
-> It ends up in the magic 9.3 m2 wing area I have ended up from many directions already several times before.
Historical data
I have in our svn by the way a OpenOffice.org spreadsheet about historical data about the basic design parameters for aircraft. There are just couple of aircraft currently in the list, but I will add more later and also you can help, you can send me more lines to the sheet, just take the sheet as a template and fill your lines and send it to me karoliina dot t dot salminen at gmail dot com. I will copy-paste your additions to the table. I am particularly interested in fast composite aircraft and not so interested in the parameters of tube and fabric aircraft or metal aircraft (except interesting ones, like RV). All data even for fabric and tube, is welcome of course, but I wanted to let you know what I am interested in the most.
Here is the spreadsheet in OpenOffice.org format:
WeightAndBasicParametersHistoricalStatistics.ods
Here is the current version of the spreadsheet in PDF-format for quick viewing:
WeightAndBasicParametersHistoricalStatistics.pdf
Here is the spreadsheet in OpenOffice.org format:
WeightAndBasicParametersHistoricalStatistics.ods
Here is the current version of the spreadsheet in PDF-format for quick viewing:
WeightAndBasicParametersHistoricalStatistics.pdf
Wednesday, May 6, 2009
Fuselage shape optimization
I decided to do svn up for QFLR5 and was delighted that it has progressed further. I decided to try out fuselage shapes this time because it turned out that QFLR5 now allows larger airfoil thicknesses than 20%. Therefore here is a 26% fuselage shape I created today.
Here is how I started it:
1. I took NLF414F airfoil which I know to have very low drag value at 10 million reynolds number.
2. I decambered to it to zero camber
3. I changed thickness to 26%
4. I changed leading edge radius: 30% from leading edge, 0.8 ratio.

The simulation result gives very low Cd-value. The problem in reality is that because of all intersections, and a hatch where one has to enter the craft, the transition point is not that great as predicted by the program most likely.
Here is another simulation, transition forced at 40% chord. The Reynolds number is the same, 41 million with mach 0.29:

I further adjusted the leading edge radius, from the above, I reduced it to 0.8 again.
Here is the result KSNLFFUSELAGE3:

The simulated polar for the NLFFUSELAGE3:

Obviously the fuselage is supposed to be flown at zero angle of attack on cruise flight, but for slight side slip situations it is good to know how the drag rises on the fuselage. It also affects to the stability negatively (for example because the lift slope is not at all linear).
Potential improvement idea for use in non-steady flight: widen the low drag bucket a bit.
The airfoil shape as a axisymmetric fuselage (or as a generic pod, this works also as a engine pod), 3D illustration:

And this is how it looks from inside:

Structurally the pod requires thicker boom than the optimum and unfortunately the drag will be larger than the simulated one for the pod alone.
Here is how I started it:
1. I took NLF414F airfoil which I know to have very low drag value at 10 million reynolds number.
2. I decambered to it to zero camber
3. I changed thickness to 26%
4. I changed leading edge radius: 30% from leading edge, 0.8 ratio.

The simulation result gives very low Cd-value. The problem in reality is that because of all intersections, and a hatch where one has to enter the craft, the transition point is not that great as predicted by the program most likely.
Here is another simulation, transition forced at 40% chord. The Reynolds number is the same, 41 million with mach 0.29:

I further adjusted the leading edge radius, from the above, I reduced it to 0.8 again.
Here is the result KSNLFFUSELAGE3:

The simulated polar for the NLFFUSELAGE3:

Obviously the fuselage is supposed to be flown at zero angle of attack on cruise flight, but for slight side slip situations it is good to know how the drag rises on the fuselage. It also affects to the stability negatively (for example because the lift slope is not at all linear).
Potential improvement idea for use in non-steady flight: widen the low drag bucket a bit.
The airfoil shape as a axisymmetric fuselage (or as a generic pod, this works also as a engine pod), 3D illustration:

And this is how it looks from inside:

Structurally the pod requires thicker boom than the optimum and unfortunately the drag will be larger than the simulated one for the pod alone.
Friday, April 24, 2009
Lentokoneen aerodynaaminen suunnittelu -luento 5.5.2009 SIL-luokka klo 17
Malmin ilmailukerho (MIK) jarjestaa Malmilla SIL-luokassa 5.5.2009 aiheena lentokoneen aerodynaaminen suunnittelu. Luennoitsijana Juha Karjalainen TKK:lta. Blogin lukijat ovat lampimasti tervetulleita Malmin Ilmailukerhon jasenten lisaksi. Kieli: suomi. Tilaisuuteen on vapaa paasy.
In English: There is a lecture about aerodynamics arranged at Malmi SIL class 5th May 2009. The language in the lecture is Finnish and the lecturer is going to be Juha Karjalainen from Helsinki University of Technology.
In English: There is a lecture about aerodynamics arranged at Malmi SIL class 5th May 2009. The language in the lecture is Finnish and the lecturer is going to be Juha Karjalainen from Helsinki University of Technology.
Wednesday, March 4, 2009
OT: MIK lectures event Today evening 18-21 at Helsinki-Malmi airport/SIL class room
Off-topic: This is just for those who read this blog but are not reading my other blogs and are located in Helsinki area Finland. We have a flying club evening event Today at Malmi airport in the SIL class, which is located in the Suomen ilmailuliitto's building next to the SIL-shop. There will be two presentations - one about flying ultralight aircraft (for PPL-pilots) and another about water flying. The lectures are in Finnish so it may not be too useful for non-Finnish speaking people to come, but if there are Finnish readers who want to join, feel free. The event is free and available to everyone. There are people present from both MIK (Malmin Ilmailukerho) and MILK (Mäntsälän ilmailukerho), so if you want to meet representatives of either clubs, you are very welcome. Lecturers today are Ari Nikkinen / MILK (Mäntsälän ilmailukerho) and Tom Arppe / EUT (Experimental and Ultralight association).
Tuesday, March 3, 2009
Monday, March 2, 2009
Will it climb?

I created new spreadsheet for calculating climb rate at sea level. I created it to investigate single engine situation in a quick way.
You can download it from here:
climbcalc.ods
WARNING! You have to know what input values you enter, otherwise the results will be bogus. For example the value of K depends on aspect ratio and e.
Friday, February 27, 2009
Aircraft range calculator

You can download it from here (it is in the katix.org gforge svn):
RangeCalculator.ods
Some calculated results:
Target range = 1500 nm
Fuel consumption = 31.5 liters/h (2 x Rotax 912ULS, with economy cruise power)
[kts] [h] [l] [kg]
Speed Endurance required Fuel liters Fuel weight
100 15 472.47 335.45
110 13.64 429.52 304.96
120 12.5 393.73 279.55
130 11.54 363.44 258.04
140 10.71 337.48 239.61
150 10 314.98 223.64
160 9.38 295.29 209.66
170 8.82 277.92 197.33
180 8.33 262.48 186.36
190 7.89 248.67 176.56
200 7.5 236.24 167.73
210 7.14 224.99 159.74
220 6.82 214.76 152.48
230 6.52 205.42 145.85
240 6.25 196.86 139.77
250 6 188.99 134.18
260 5.77 181.72 129.02
270 5.56 174.99 124.24
280 5.36 168.74 119.81
290 5.17 162.92 115.67
Friday, February 20, 2009
KS20 airfoil simulation
KS20:

Cl - Cd(low reynolds numbers also included, plus also flapped version (+10deg and +20 deg)

L/D vs. alpha:

Cm vs. Alpha:

Cl - alpha:

Printable profile picture of KS20 (black on white background):

KS20.dat Airfoil file for QFLR5, XFLR5 or Xfoil

Cl - Cd(low reynolds numbers also included, plus also flapped version (+10deg and +20 deg)

L/D vs. alpha:

Cm vs. Alpha:

Cl - alpha:

Printable profile picture of KS20 (black on white background):

QFLR5_v.0001
Calculated polar for: KS20
1 1 Reynolds number fixed Mach number fixed
xtrf = 1.000 (top) 1.000 (bottom)
Mach = 0.270 Re = 5.000 e 6 Ncrit = 9.000
alpha CL CD CDp CM Top Xtr Bot Xtr Cpmin Chinge XCp
------- -------- --------- --------- -------- ------- ------- -------- --------- ---------
-2.500 0.0172 0.00639 0.00156 -0.0630 0.5734 0.1263 -0.9628 0.0000 3.9974
-2.000 0.0779 0.00594 0.00135 -0.0638 0.5687 0.2065 -0.7727 0.0000 1.0832
-1.500 0.1376 0.00529 0.00111 -0.0647 0.5613 0.3515 -0.6885 0.0000 0.7246
-1.000 0.1985 0.00466 0.00091 -0.0657 0.5560 0.4943 -0.7241 0.0000 0.5818
-0.500 0.2604 0.00434 0.00082 -0.0667 0.5474 0.5909 -0.7638 0.0000 0.5048
0.000 0.3235 0.00430 0.00084 -0.0677 0.5380 0.6224 -0.8063 0.0000 0.4565
0.500 0.3863 0.00438 0.00088 -0.0686 0.5260 0.6346 -0.8489 0.0000 0.4238
1.000 0.4491 0.00445 0.00094 -0.0696 0.5127 0.6478 -0.8954 0.0000 0.4002
1.500 0.5115 0.00461 0.00102 -0.0704 0.4945 0.6510 -0.9563 0.0000 0.3823
2.000 0.5732 0.00475 0.00111 -0.0712 0.4723 0.6587 -1.0304 0.0000 0.3682
2.500 0.6344 0.00497 0.00124 -0.0719 0.4472 0.6628 -1.1188 0.0000 0.3567
3.000 0.6941 0.00529 0.00142 -0.0723 0.4114 0.6656 -1.2143 0.0000 0.3470
3.500 0.7516 0.00577 0.00168 -0.0724 0.3616 0.6675 -1.3096 0.0000 0.3385
4.000 0.8098 0.00619 0.00194 -0.0726 0.3230 0.6691 -1.4113 0.0000 0.3313
4.500 0.8664 0.00670 0.00226 -0.0725 0.2804 0.6702 -1.5275 0.0000 0.3247
5.000 0.9229 0.00719 0.00260 -0.0724 0.2437 0.6718 -1.6463 0.0000 0.3189
KS20.dat Airfoil file for QFLR5, XFLR5 or Xfoil
Monday, February 16, 2009
Sunday, February 15, 2009
Simulations: Althaus AH 94-145 vs. AH 95-160
Monday, February 9, 2009
Interesting BWB links
www.aoe.vt.edu/research/groups/bwb/papers/TheBWBAircraft.pdf
http://silentaircraft.org/object/download/1931/doc/AIAA-2006-241-725.pdf">silentaircraft.org/object/download/1931/doc/AIAA-2006-241-725.pdf
http://ntrs.nasa.gov/archive/nasa/casi.ntrs.nasa.gov/20050182126_2005180630.pdf">ntrs.nasa.gov/archive/nasa/casi.ntrs.nasa.gov/20050182126_2005180630.pdf
http://www.onera.fr/daap/ailes-volantes/aerodynamic-optimization-of-subsonic-flying-wing-configurations.pdf"> www.onera.fr/daap/ailes-volantes/aerodynamic-optimization-of-subsonic-flying-wing-configurations.pdf
silentaircraft.org/object/download/1945/doc/AIAA-2007-453-759.pdf">silentaircraft.org/object/download/1945/doc/AIAA-2007-453-759.pdf
http://silentaircraft.org/object/download/1931/doc/AIAA-2006-241-725.pdf">silentaircraft.org/object/download/1931/doc/AIAA-2006-241-725.pdf
http://ntrs.nasa.gov/archive/nasa/casi.ntrs.nasa.gov/20050182126_2005180630.pdf">ntrs.nasa.gov/archive/nasa/casi.ntrs.nasa.gov/20050182126_2005180630.pdf
http://www.onera.fr/daap/ailes-volantes/aerodynamic-optimization-of-subsonic-
silentaircraft.org/object/download/1945/doc/AIAA-2007-453-759.pdf">silentaircraft.org/object/download/1945/doc/AIAA-2007-453-759.pdf
Sunday, February 8, 2009
Gforge site for open source aircraft projects
Our gforge site can host in addition to software projects, also now open source aircraft projects. If you are interested in open source aircraft idea, feel free to join the forces at:
http://gforge.katix.org/gf/
I have setted up two my open source airplane projects there (they don't have much yet, but one has to start from somewhere, right?). So if you are interested in joining one of these existing projects, or you have a promising own project which you would like to share with other people, here is your chance. Register yourself and propose a project. I am the admin and approving you and your project proposals.
The motivation to join could be to get some fame. In the software field, open source developers are at the top of the ranking scale. This could be the case in the other fields too. You can make sure that you don't miss the train by joining and contributing to projects or by creating and sharing your own projects with everybody. Also here is your chance to collaborate and get results. Getting things done with large number of eyes looking after the same thing is more likely than everybody doing their things alone.
The site requires approval from site admins, so please make sure you describe your project in enough detail to get it approved. We do approve potential projects.
http://gforge.katix.org/gf/
I have setted up two my open source airplane projects there (they don't have much yet, but one has to start from somewhere, right?). So if you are interested in joining one of these existing projects, or you have a promising own project which you would like to share with other people, here is your chance. Register yourself and propose a project. I am the admin and approving you and your project proposals.
The motivation to join could be to get some fame. In the software field, open source developers are at the top of the ranking scale. This could be the case in the other fields too. You can make sure that you don't miss the train by joining and contributing to projects or by creating and sharing your own projects with everybody. Also here is your chance to collaborate and get results. Getting things done with large number of eyes looking after the same thing is more likely than everybody doing their things alone.
The site requires approval from site admins, so please make sure you describe your project in enough detail to get it approved. We do approve potential projects.
ZyggerDesigner gforge project (svn repository) is now up

Kate setted up gforge on our server, so I decided to put my conceptual design tool to a subversion repository. You can find it here:
http://gforge.katix.org/gf/project/zdesigner/
Contributions to the software is very welcome. You can register to the Katix gforge and join the project if you think you can contribute. I am looking for aeronautical engineers and students to help with the software development. There may be some equations which have errors. You can help with pointing them out. The bug tracker should be used for that purpose.
Also some extra eyes reviewing the code (it is currently quite quickly hacked together) would be helpful, if you are not specialized in aircraft conceptual design, but you are good with C++ and Qt and you have too much time, feel free to join and start filing bugs about bad code. If you have even more time, feel free to write and suggest patches that fixes the issues. I am not looking for comments about indentation (if I see that kind of bugs too often, I will resolve them as invalid) etc., but rather memory leaks, something done really wrong with Qt - real issues in other words.
The code is licensed under GPL version 3 or any later version -license.
Anonymous svn access to the repository (without commit privileges):
svn checkout http://katix.org/svn/zdesigner/trunk zdesigner
Saturday, February 7, 2009
NLF215F considerations, Cl for different conditions
My earlier post about the NLF215F simulations with XFLR5, the related parameters for aircraft would be in the use case (one iteration of thinking):
- low altitude cruise:
* altitude = 12000 ft
* W/S = 22 lbs/sqft
* Clcruise = 0.41
* NLF215F flap in the -10 degrees position, gap seals closed
- high altitude cruise:
* altitude = 36000 ft
* W/S = 22 lbs/sqft
* Clcruise = 0.96
* NLF215F flap in the 0 degree position, gap seals closed
- extreme high altitude cruise
* some fuel burned already -> W/S reduced to 21 lbs/sqft
* altitude = 46000 ft
* W/S = 21 lbs/sqft
* Clcruise = 1.48
* NLF215F flap in the 0 degrees position, gap seals closed
- approach
* 1 slot open
* W/S = 15 lbs/sqft
* altitude = 1000 ft
* Cl = 1.1, V = 75 kts (at gross weight, W/S 22 lbs/sqft)
* Cl = 1.1, V = 65 kts (when fuel tanks nearly empty, W/S 15 lbs/sqft)
* NLF215F flap in the +10 degrees position, 1 slot open
- landing
* 2 slots open
- low altitude cruise:
* altitude = 12000 ft
* W/S = 22 lbs/sqft
* Clcruise = 0.41
* NLF215F flap in the -10 degrees position, gap seals closed
- high altitude cruise:
* altitude = 36000 ft
* W/S = 22 lbs/sqft
* Clcruise = 0.96
* NLF215F flap in the 0 degree position, gap seals closed
- extreme high altitude cruise
* some fuel burned already -> W/S reduced to 21 lbs/sqft
* altitude = 46000 ft
* W/S = 21 lbs/sqft
* Clcruise = 1.48
* NLF215F flap in the 0 degrees position, gap seals closed
- approach
* 1 slot open
* W/S = 15 lbs/sqft
* altitude = 1000 ft
* Cl = 1.1, V = 75 kts (at gross weight, W/S 22 lbs/sqft)
* Cl = 1.1, V = 65 kts (when fuel tanks nearly empty, W/S 15 lbs/sqft)
* NLF215F flap in the +10 degrees position, 1 slot open
- landing
* 2 slots open
Friday, February 6, 2009
NLF vs. turbulent

I ran some simulations for different airfoils in the same condition:
- cruise at medium low altitude, Cl = 0.4, speed = 0.26 mach, Re = 4000000, wing loading >= 20 lbs/sqft.
I first simulated a large number of different airfoils, but finally only picked the couple of NACAs and the NLF215F with -10 degree negative cruise flap and without.
The NLF215F has a clearly better overall performance all over the Cl range what it comes to Cd. Also the pitching moment of this airfoil becomes low when the cruise flap is at -10 degrees.
Labels:
airfoil,
airfoil simulation,
NLF vs. turbulent,
XFLR5,
xfoil
Thursday, February 5, 2009
How to use XFLR5 in Linux
The XLFR5 is a easier to use interface built on top of the X-foil engine. The X-foil also features wing and whole airplane analysis functions.
The downside of the program has been that is only available for Windows. However, it can be run nowadays in Linux without porting the program to e.g. Qt (which is a big task), so in the mean time before any cross-platform version appears, you can live with the wine in Linux environment:
- Make sure your wine version is a pretty recent one, version greater than 1.0.
I am using the Ubuntu Intrepid version. apt-cache policy wine reports the following:
wine:
Installed: 1.0.1-0ubuntu2
Candidate: 1.0.1-0ubuntu2
Version table:
*** 1.0.1-0ubuntu2 0
500 http://archive.ubuntu.com intrepid/universe Packages
100 /var/lib/dpkg/status
W: Duplicate sources.list entry http://archive.ubuntu.com intrepid/universe Packages (/var/lib/apt/lists/archive.ubuntu.com_ubuntu_dists_intrepid_universe_binary-i386_Packages)
W: Duplicate sources.list entry http://archive.ubuntu.com intrepid/multiverse Packages (/var/lib/apt/lists/archive.ubuntu.com_ubuntu_dists_intrepid_multiverse_binary-i386_Packages)
If you are running the latest stable Ubuntu (Intrepid - 8.10), you can use the Ubuntu supplied one and it will work fine with XFLR5. However, if you are running Ubuntu Hardy or some other distro that does not have the post-1.0 version available, you can install it from winehq repository. For debian based distros like Ubuntu, the instructions can be found from here:
http://www.winehq.org/download/deb
Our living room computer is not yet updated and it is still running the older Hardy. I updated the wine by adding the following line to /etc/apt/sources.list:
deb http://wine.budgetdedicated.com/apt hardy main #WineHQ - Ubuntu 8.04 "Hardy Heron"
Then I did apt-get update and apt-get install wine
The new version of wine got installed and the XFLR5 started working fine.
Download the XFLR5 from here:
http://xflr5.sourceforge.net/xflr5.htm
Go to download page and click download. At the time of writing this, the 4.15 was the latest version.
Download the zip file XFLR5_v415.zip to a new subfolder into your home directory, because the zip file does not contain directories and when you unzip it, if you was in your home directory, you get the package contents directly there which messes up your home with lots of unnecessary files.
Run the XFLR5_Setup.exe by typing on a terminal:
wine ./XFLR5_Setup.exe
The setup runs and finishes.
After this you can notice that a new entry appeared to your Applications menu (in Gnome):
Applications - Wine
Select submenu Programs, and there XFLR5 and on that submenu XFLR5.
XFLR5 should now start successfully.
It works on my computer without problems now.
The downside of the program has been that is only available for Windows. However, it can be run nowadays in Linux without porting the program to e.g. Qt (which is a big task), so in the mean time before any cross-platform version appears, you can live with the wine in Linux environment:
- Make sure your wine version is a pretty recent one, version greater than 1.0.
I am using the Ubuntu Intrepid version. apt-cache policy wine reports the following:
wine:
Installed: 1.0.1-0ubuntu2
Candidate: 1.0.1-0ubuntu2
Version table:
*** 1.0.1-0ubuntu2 0
500 http://archive.ubuntu.com intrepid/universe Packages
100 /var/lib/dpkg/status
W: Duplicate sources.list entry http://archive.ubuntu.com intrepid/universe Packages (/var/lib/apt/lists/archive.ubuntu.com_ubuntu_dists_intrepid_universe_binary-i386_Packages)
W: Duplicate sources.list entry http://archive.ubuntu.com intrepid/multiverse Packages (/var/lib/apt/lists/archive.ubuntu.com_ubuntu_dists_intrepid_multiverse_binary-i386_Packages)
If you are running the latest stable Ubuntu (Intrepid - 8.10), you can use the Ubuntu supplied one and it will work fine with XFLR5. However, if you are running Ubuntu Hardy or some other distro that does not have the post-1.0 version available, you can install it from winehq repository. For debian based distros like Ubuntu, the instructions can be found from here:
http://www.winehq.org/download/deb
Our living room computer is not yet updated and it is still running the older Hardy. I updated the wine by adding the following line to /etc/apt/sources.list:
deb http://wine.budgetdedicated.com/apt hardy main #WineHQ - Ubuntu 8.04 "Hardy Heron"
Then I did apt-get update and apt-get install wine
The new version of wine got installed and the XFLR5 started working fine.
Download the XFLR5 from here:
http://xflr5.sourceforge.net/xflr5.htm
Go to download page and click download. At the time of writing this, the 4.15 was the latest version.
Download the zip file XFLR5_v415.zip to a new subfolder into your home directory, because the zip file does not contain directories and when you unzip it, if you was in your home directory, you get the package contents directly there which messes up your home with lots of unnecessary files.
Run the XFLR5_Setup.exe by typing on a terminal:
wine ./XFLR5_Setup.exe
The setup runs and finishes.
After this you can notice that a new entry appeared to your Applications menu (in Gnome):
Applications - Wine
Select submenu Programs, and there XFLR5 and on that submenu XFLR5.
XFLR5 should now start successfully.
It works on my computer without problems now.
First attempt on airfoil design

I created these:
KaroliinaNLF1016.dat
KaroliinaNLF1016F-5.dat
X-foil is predicting for KaroliinaNLF1016F-5 (-5 degrees cruise flap for low altitude) exactly what I was looking for. The KaroliinaNLF1016 is decambered and a bit thickened (16%) version of NASA NLF1015. According to quick analysis, laminar bucket has same shape as NLF1015 has, L/D and minimum Cd is the same, but it has been lowered to a bit lower Cl and also the useful Cl is a bit lower than on NLF1015. However, this way, the unacceptable cruise performance at low altitude theoretically gets acceptable. I need to experiment more and try out with different Re numbers. I was testing at only Re = 1000000 since that is where I was targeting the high altitude cruise. However, the Re is a lot higher at low altitude, gets easily to 5000000, so I will need to try more analysis on the airfoil tomorrow.
Wednesday, February 4, 2009
Clouds all over the world
Wanna see the current cloud situation?
I accidentally found this, it is pretty cool site, satellite imagery is updated daily and it covers the whole Earth:
http://www.flashearth.com/
I accidentally found this, it is pretty cool site, satellite imagery is updated daily and it covers the whole Earth:
http://www.flashearth.com/
Sunday, February 1, 2009
Saturday, January 31, 2009
Hybrid aircraft
The idea of the system comprises of a turbo generator per engine and an additional electric motor behind the tail.
Configuration:
Two gasoline engines, one per wing.
One Brushless DC electric motor, behind the tail, engine size around 15 kW. Does not require any drive shaft because the motor itself is so small and lightweight, that it can be attacted directly to the tail.
Battery that can deliver full power to the electric motor for 3 minutes.
Motor controller for each electric motor.
Possible additions:
Two wing tip turbines, one per each wing tip. Electric motor size ~5 kW.
These can produce power on cruise for the middle pusher motor.
The center pusher motor could drive a unducted fan which would have diameter around 1/3 of the diameter of the fuselage body. See NASA tech paper wake propeller, why. The fan would require adjustable pitch for each blade, so it could be changed from climb condition to cruise condition for the cruise phase (otherwise it would cause drag penalty).
Additional idea:
- the wing tip turbines could be used in case of engine failure for thrust vectoring - one small wing tip engine producing thrust could make the asymmetric thrust condition symmetric without causing drag penalty with deflected rudder.
Configuration:
Two gasoline engines, one per wing.
One Brushless DC electric motor, behind the tail, engine size around 15 kW. Does not require any drive shaft because the motor itself is so small and lightweight, that it can be attacted directly to the tail.
Battery that can deliver full power to the electric motor for 3 minutes.
Motor controller for each electric motor.
Possible additions:
Two wing tip turbines, one per each wing tip. Electric motor size ~5 kW.
These can produce power on cruise for the middle pusher motor.
The center pusher motor could drive a unducted fan which would have diameter around 1/3 of the diameter of the fuselage body. See NASA tech paper wake propeller, why. The fan would require adjustable pitch for each blade, so it could be changed from climb condition to cruise condition for the cruise phase (otherwise it would cause drag penalty).
Additional idea:
- the wing tip turbines could be used in case of engine failure for thrust vectoring - one small wing tip engine producing thrust could make the asymmetric thrust condition symmetric without causing drag penalty with deflected rudder.
Friday, January 30, 2009
Thursday, January 29, 2009
X-plane as educational program
It seems that X-plane educates aerodynamics, what to expect and think about different things. I was originally saying that I am not so interested in transonic region but rather interested in high altitude. I have been reading about these, but some little things like tinkering with X-plane can cause heureka moments.
And here is what happened:
I have a model of my twin concept in X-plane simulator (obviously, why wouldn't I). So I set in the latest incarnation the engine critical altitude to 50000 ft (which is feasible with two turbos in cascade plus the mentioned electric turbo compounding). I used 110 hp per side (equivalent of Rotax 912ULS equipped with two turbos doing turbo normalization plus intercooler and after cooler).
I was reading Roskam couple of days ago and noticed that the transonic drag is not a problem if the speed is mach 0.2 or below or not that much above that, e.g. 0.3-0.4 is still quite fine. So I was thinking that maybe it doesn't get that high that it would become a consideration.
So so obviously, I put the plane model to climb to 55000 ft with autopilot. I had previously added the mach meter to the hud. I came back checking how it flies after couple of tens of minutes. And oops: mach 0.56 when level at 55000 ft. The IAS was barely 100 kts. TAS was a quite a bit higher.
Then, I was thinking what happens to the Reynolds number. Indeed it gets smaller with altitude increasing. But interesting thing is what really happens, to which number it gets. I verified with atmosphere calculator, that indeed, the interesting Re range for this kind of concept with the AR=14 wing, it becomes 600000 - 1600000. That is _very_ low for an aircraft, which is full size and not a RC-model. So the low Re becomes after all a major consideration.
How a plane with AR=14 flies at 55000 ft? It requires _full_ trim aft (meaning nose high) to get the plane keep level - in this model. It became quite apparent that indeed, the tail volume coefficient is a more major concern at high altitude than at low altitude. And the control authority that felt fine at low altitude was not so fine at high altitude.
So this is what we have:
- High performance low Re airfoil is very necessary
- Cd at high lift coefficient is an important design point, the airfoil needs to be designed so that it gives high L/D at high lift coefficient rather than at low lift coefficient like for example NLF414F is targeting.
- A big tail with long enough moment arm
- Propeller with large diameter and possibly more blades than usual, e.g. 5 blades
- And of course, two turbos, intercooler, aftercooler, generator, battery, electric motor and a shaft between the prop and the engine.
Btw, my model is not yet available for download because it is not perfect, and it has couple of problems. It is very hard to get the splines right with straight sections edited by hand, and e.g. engine nacelles look really terrible at the moment. Anyway, it is a fun way for trying out things in practice.
And here is what happened:
I have a model of my twin concept in X-plane simulator (obviously, why wouldn't I). So I set in the latest incarnation the engine critical altitude to 50000 ft (which is feasible with two turbos in cascade plus the mentioned electric turbo compounding). I used 110 hp per side (equivalent of Rotax 912ULS equipped with two turbos doing turbo normalization plus intercooler and after cooler).
I was reading Roskam couple of days ago and noticed that the transonic drag is not a problem if the speed is mach 0.2 or below or not that much above that, e.g. 0.3-0.4 is still quite fine. So I was thinking that maybe it doesn't get that high that it would become a consideration.
So so obviously, I put the plane model to climb to 55000 ft with autopilot. I had previously added the mach meter to the hud. I came back checking how it flies after couple of tens of minutes. And oops: mach 0.56 when level at 55000 ft. The IAS was barely 100 kts. TAS was a quite a bit higher.
Then, I was thinking what happens to the Reynolds number. Indeed it gets smaller with altitude increasing. But interesting thing is what really happens, to which number it gets. I verified with atmosphere calculator, that indeed, the interesting Re range for this kind of concept with the AR=14 wing, it becomes 600000 - 1600000. That is _very_ low for an aircraft, which is full size and not a RC-model. So the low Re becomes after all a major consideration.
How a plane with AR=14 flies at 55000 ft? It requires _full_ trim aft (meaning nose high) to get the plane keep level - in this model. It became quite apparent that indeed, the tail volume coefficient is a more major concern at high altitude than at low altitude. And the control authority that felt fine at low altitude was not so fine at high altitude.
So this is what we have:
- High performance low Re airfoil is very necessary
- Cd at high lift coefficient is an important design point, the airfoil needs to be designed so that it gives high L/D at high lift coefficient rather than at low lift coefficient like for example NLF414F is targeting.
- A big tail with long enough moment arm
- Propeller with large diameter and possibly more blades than usual, e.g. 5 blades
- And of course, two turbos, intercooler, aftercooler, generator, battery, electric motor and a shaft between the prop and the engine.
Btw, my model is not yet available for download because it is not perfect, and it has couple of problems. It is very hard to get the splines right with straight sections edited by hand, and e.g. engine nacelles look really terrible at the moment. Anyway, it is a fun way for trying out things in practice.
Labels:
aircraft concept,
heureka,
high altitude,
twin,
x-plane,
X-plane model
Monday, January 26, 2009
Hybrid turbo compounding
Kate invented one day that why the turbo compounding could not be implemented with electric motors, because that way the usually unfeasible gearbox from normal turbo compounding becomes unnecessary and the gearing is instead implemented with the electric motor and the generator where the generator rotates at higher revolutions than the motor that is used to decrease the load the combustion engine sees.
We were in assumption that this was a new invention, but it seems that it has been used in heavy machinery already, e.g. by Catepillar. This in turn also means that it is feasible.
The challenge would be how to place the generator to the shaft of the turbo. Usually turbos do not have a place where to fit the generator but they are closed packages which are not easily modifiable.
The idea would be to increase fuel efficiency with the compounding and increase the shaft horse power without loading the combustion engine anything more. The electric motor could have an additional lithium polymer batter pack which could increase the power even more on takeoff, so the plane would have on critical take off situation somewhat more power than the combustion engine can output, so in other words, for example getting 80 hp out of a 60 hp HKS700E.
This would result that using impossibly small engine power would become a possibility in a wider variety of airframes. On a twin 2 x 80 hp is a lot more than 2 x 60 hp, single engine performance on 60 hp is very poor in any case without any tricks done to increase the power temporarily.
A quite small lithium polymer battery pack would be enough since assuming 300 fpm climb rate on a single engine, this results 3 minutes to 1000 feet AGL where it should be safe to turn back to the runway and perform landing even with a very low power output of a single engine. So it would be well enough for the extra power from the battery pack last only for 3 minutes. This kind of battery pack would not be that heavy, and the brushless DC electric motor is also pretty lightweight.
Any comments on this?
We were in assumption that this was a new invention, but it seems that it has been used in heavy machinery already, e.g. by Catepillar. This in turn also means that it is feasible.
The challenge would be how to place the generator to the shaft of the turbo. Usually turbos do not have a place where to fit the generator but they are closed packages which are not easily modifiable.
The idea would be to increase fuel efficiency with the compounding and increase the shaft horse power without loading the combustion engine anything more. The electric motor could have an additional lithium polymer batter pack which could increase the power even more on takeoff, so the plane would have on critical take off situation somewhat more power than the combustion engine can output, so in other words, for example getting 80 hp out of a 60 hp HKS700E.
This would result that using impossibly small engine power would become a possibility in a wider variety of airframes. On a twin 2 x 80 hp is a lot more than 2 x 60 hp, single engine performance on 60 hp is very poor in any case without any tricks done to increase the power temporarily.
A quite small lithium polymer battery pack would be enough since assuming 300 fpm climb rate on a single engine, this results 3 minutes to 1000 feet AGL where it should be safe to turn back to the runway and perform landing even with a very low power output of a single engine. So it would be well enough for the extra power from the battery pack last only for 3 minutes. This kind of battery pack would not be that heavy, and the brushless DC electric motor is also pretty lightweight.
Any comments on this?
Saturday, January 24, 2009
MGS L285 mix ratio
The ratios for L285, H285, H287 are:
100:50 by volume
100:40 by weight
I am doing some little layup today, so I decided to write the mixing ratio to my blog. I always tend to forget it and have to search from the MGS documentation. Now it is here in my blog. This same ratio applies to my MGS L285/H287.
100:50 by volume
100:40 by weight
I am doing some little layup today, so I decided to write the mixing ratio to my blog. I always tend to forget it and have to search from the MGS documentation. Now it is here in my blog. This same ratio applies to my MGS L285/H287.
Pushing the limits
Why am I interested in pushing the limits instead of doing a known safe solution (meaning thinking more than usual aerodynamics, low weight, low power, low production cost, manufacturing technology, integrated advanced avionics)?
This could be asked with a counter question: why not? What would be the motivation of replicating some existing aircraft with existing technology with learning nothing new?
Someone might say that because of business, to sell these things. But to be sincere, I believe that this business scene is already congested, and it there is anecdotal evidence that the profitability of this business is questionable at times. And there are already number of manufacturers which are doing this and their planes are just fine. If one wants an average plane which is not supposed to push any limits, there is plenty of selection with all kinds of colors, at least one can choose if the plane is white or white or maybe metallic gray, and gluing red or blue tape stripes is optional.
If we look back 50 years and think what has been happening in general aviation. We can conclude that we are entering yet another year with virtually a very little or no progress. Engine technology is still the same, aerodynamics have only moderately improved (laminar flow wings are nowadays somewhat utilized (Cirrus and Cessna 400), but not laminar flow fuselages) but not much, and avionics are still the same (but only gradually improved) rather than inventing a question for the answer that this is always been done that way and answering to it before it is asked.
One could ask, what is there to improve? Why to change anything. If one has nothing better to offer, then the whole venture is worthless. The easiest way to copy and not learn anything new is not to design own aircraft, but buy an existing one. If time spent for engineering is counted with any kind of monetary value, then purchasing an existing aircraft is potentially also the cheapest way to get flying. It is also the safest way, and the chances of big disappointment is small. You get what you pay and it is potentially a good compromise and biggest bugs are already fixed.
But one thing is that for some, pushing the limits is the meaning of life.
I see that the future of general aviation is not very bright without radical new designs which are better performing than the current aircraft, a lot more economical than current models, and essentially less expensive to buy and operate than the current aircraft.
This requires couple of breakthroughs to happen. I am not interested in solving all of them, I do not have unlimited time and can not have solution for everything.
I rather prefer to think everything through a filter which is the compromise I have found best suitable during the couple of years I have been thinking what do I want and now I am finding reasons why I want it. As the answer to the question can not be seen as a singularity, to make the others with a different experience base and collection of individual goals to understand the questions and the answers in this specific case in a give time fragment, can be seen as a challenging endeavor which leads to a setup where all the sides of the multidimensional coin are not fully seen.
When I know what do I want, I can more easily tackle down, what is the minimum resemblance to what I want which still is an acceptable compromise but is feasible technologically and economically and evidently this is a moving target which evolves in the flow of time.
The limits being pushed also evolve but the end result is a snapshot of the broken limits of that time and the frozen design parameters of the evolving concept and today's limits no longer exist as limits but are by then generally accepted known solutions. If this did not take place, the eventual outdatedness of the design would outweight the thought benefits of the whole reason of doing it in the first place and the understanding of the question of why to do it would be remaining essentially unanswered in a light of the evolving circumstances where the answers are integrating variables rather than constants.
The only sensible way to follow the flow of things is to ensure being a step further than the current state of the art, otherwise the train left the station before it was built and one arrived there to travel to a place which no longer exists. This way the coin has a chance to drop the right side up in a place where the relative up is defined by the eye of the beholder, which by definition, defines the answer to the questions who I am and what do I want.
This could be asked with a counter question: why not? What would be the motivation of replicating some existing aircraft with existing technology with learning nothing new?
Someone might say that because of business, to sell these things. But to be sincere, I believe that this business scene is already congested, and it there is anecdotal evidence that the profitability of this business is questionable at times. And there are already number of manufacturers which are doing this and their planes are just fine. If one wants an average plane which is not supposed to push any limits, there is plenty of selection with all kinds of colors, at least one can choose if the plane is white or white or maybe metallic gray, and gluing red or blue tape stripes is optional.
If we look back 50 years and think what has been happening in general aviation. We can conclude that we are entering yet another year with virtually a very little or no progress. Engine technology is still the same, aerodynamics have only moderately improved (laminar flow wings are nowadays somewhat utilized (Cirrus and Cessna 400), but not laminar flow fuselages) but not much, and avionics are still the same (but only gradually improved) rather than inventing a question for the answer that this is always been done that way and answering to it before it is asked.
One could ask, what is there to improve? Why to change anything. If one has nothing better to offer, then the whole venture is worthless. The easiest way to copy and not learn anything new is not to design own aircraft, but buy an existing one. If time spent for engineering is counted with any kind of monetary value, then purchasing an existing aircraft is potentially also the cheapest way to get flying. It is also the safest way, and the chances of big disappointment is small. You get what you pay and it is potentially a good compromise and biggest bugs are already fixed.
But one thing is that for some, pushing the limits is the meaning of life.
I see that the future of general aviation is not very bright without radical new designs which are better performing than the current aircraft, a lot more economical than current models, and essentially less expensive to buy and operate than the current aircraft.
This requires couple of breakthroughs to happen. I am not interested in solving all of them, I do not have unlimited time and can not have solution for everything.
I rather prefer to think everything through a filter which is the compromise I have found best suitable during the couple of years I have been thinking what do I want and now I am finding reasons why I want it. As the answer to the question can not be seen as a singularity, to make the others with a different experience base and collection of individual goals to understand the questions and the answers in this specific case in a give time fragment, can be seen as a challenging endeavor which leads to a setup where all the sides of the multidimensional coin are not fully seen.
When I know what do I want, I can more easily tackle down, what is the minimum resemblance to what I want which still is an acceptable compromise but is feasible technologically and economically and evidently this is a moving target which evolves in the flow of time.
The limits being pushed also evolve but the end result is a snapshot of the broken limits of that time and the frozen design parameters of the evolving concept and today's limits no longer exist as limits but are by then generally accepted known solutions. If this did not take place, the eventual outdatedness of the design would outweight the thought benefits of the whole reason of doing it in the first place and the understanding of the question of why to do it would be remaining essentially unanswered in a light of the evolving circumstances where the answers are integrating variables rather than constants.
The only sensible way to follow the flow of things is to ensure being a step further than the current state of the art, otherwise the train left the station before it was built and one arrived there to travel to a place which no longer exists. This way the coin has a chance to drop the right side up in a place where the relative up is defined by the eye of the beholder, which by definition, defines the answer to the questions who I am and what do I want.
Thursday, January 22, 2009
Minimal twin
In the mean time, on the back of my head, I have also been thinking the twin concept. What is the minimum power feasible for the twin for being safe in single engine situation, and what can be the maximum weight and maximum wing loading of a plane which is equipped with two HKS700E engines (only 60 hp each).
Known thing is that Diamond DA42 climbs still at 22 lbs/sqft wing loading and 24 lbs/hp power loading on single engine. However, there is quite a bit more excess power on 135 hp Thielert than on a 60 hp engine. I am feeling that I am getting too optimistic results from the sizing equations with either Raymer or Anderson method.
I have estimated that the plane should not weight more than 700 kg (according to the equations) to still be able to take off and climb with single engine. This may be too optimistic figure, I have been thinking that the limit might be rather near 650 kg or maybe even a bit less.
Thinking pessimistic: the plane can have positive climb rate with 60 hp single engine mode if the gross weight is 600 kg. That gives:
600 - 55 kg - 10 kg - 55 kg - 10 kg = 470 kg for the airframe + useful load excluding engines.
For useful load, minimally needed is:
- Two big adults, 95 kg including heavy clothes per each
- 5 kg baggage per each
- 120 liters of gasoline = 85 kg
This becomes:
95 kg * 2 + 10 kg + 85 kg = 285 kg.
For the plane to be minimally useful, it must be able to carry 285 kg in addition to its own weight. There are two engines and to have useful endurance the amount of fuel has to be double the size of a single engine plane.
The airframe + systems maximum weight excluding engines then becomes:
470 kg -285 kg = 185 kg
This means that the airframe + systems excluding engine can only weight 185 kg. This is a very hard goal to achieve.
The aircraft empty weight then becomes:
185 kg + 65 kg + 65 kg = 315 kg
The empty weight to gross weight ratio becomes:
315 kg / 600 kg = 0.52
This ratio is very challenging to achieve for a twin where the airframe must be carrying in addition to the occupants instead of one engine, two engines, and their fuel.
If we could still take off at 650 kg, then this becomes:
Airframe weight can be increased with 50 kg: 185 kg + 50 kg = 235 kg
235 kg + 65 kg + 65 kg = 365 kg
Looks like now we are talkin. This looks like a figure which might be theoretically possible, even though this is still very hard goal. As seen on ultralight planes, achieving empty weight under 300 kg is very hard. Adding extra engine on top that requires aircraft that is as lightweight than best ultralights equipped, plus can still take the additional engine.
But this is just theoretical thinking and whether or not it may be feasible, the discussion can continue:
The empty weight to gross weight ratio then becomes:
365 kg / 650 kg = 0.56
Historical data shows that at least on a bit larger aircraft, the 0.56 value is pretty well achievable.
Lets consider now the performance for the 650 kg case:
Single engine produces only 60 hp power. Only the excess power can be used for climb. This means that in a side slip of asymmetric thrust and climb angle of attack, the total drag (drag due to lift + fuselage drag) must be less than the thrust of 60 hp at best climb speed with a propeller that has efficiency of 0.7 (for pessimistic evaluation, I prefer to not use 0.85) by a large margin, and then the climb rate pretty much becomes from the weight to be lifted and how much excess power is still left.
The power loading for single case would be: 23.8 lbs/hp. This would be about the same as Diamond DA42. The drag must be low in order to ensure that the power needed for level flight is small, and there is excess power for climb, even with very low power.
Then comes the disaster of increasing wing area, this increases drag, but on the other hand, increases also lift. However, to get good cruise performance on the low power, wing size should be as small as possible. So some compromise is needed here. Increase in wing loading has to be accounted with increase in aspect ratio to keep the induced drag the same. Increase of aspect ratio may increase weight, but does not necessarily always do so. For example the earlier mentioned LH10 has very light wings, despite of aspect ratio of 14. So it worths researching on this area. A good design is a synergetic design which combines couple of good things into one good compromise.
I maybe need to redo the calculation yet another time again.
Why I am thinking this?
- For a plane that I would design for myself, I could choose Rotax 912ULS, and get two used engines with about half the price of a new Rotax 912ULS. This would be roughly the cost of a pair of new HKS700E.
- However, if we think a kit-builder who wants to have a twin with shoestring budget. Many aviators are limited with budget (aviators are always rich simply does not seem to be true, and if they originally were, they no longer are after starting spending to flying). So we have been thinking of a concept of a light plane with two engines with good performance. Any twin out there, even used ones, cost many many times more than it would cost to build a plastic one with two little HKS700E engines.
- I think that twin engine aircraft are not so popular, not because they require the additional license, but because people do not opt for the additional license, because the cost of the twin is prohibitive. There is absolutely no twin out there where one could log twin engine time and which would not cost a fortune of a millionaire to own or cost a fortune of of a normal people to maintain and operate.
- It is often explained that twins are more dangerous than singles. However, the context seems to be forgotten. Single engine limits the use of the plane and with two engines, people may often go to more dangerous situations.
- And it is not only a bad thing, consider this: You live in Finland and want to visit for example Greenland. What do you do if you want to fly there by yourself and not to sit as a passenger on an Airbus? You go and start your C172 and head towards Greenland. If the one old-fashioned engine that is almost approaching car engines in reliability, that is there, quits, then you are in biiig trouble. Wouldn't it be great if there was a second engine and you could still fly even if the one failed. Even if the climb rate with single engine is poor, you could still maybe get out of there alive. Your speed would get slow, but also your fuel consumption becomes half because only one engine is drinking the fuel. You actually might make it and your relatives don't need to arrange funerals.
Any comments on this?
Known thing is that Diamond DA42 climbs still at 22 lbs/sqft wing loading and 24 lbs/hp power loading on single engine. However, there is quite a bit more excess power on 135 hp Thielert than on a 60 hp engine. I am feeling that I am getting too optimistic results from the sizing equations with either Raymer or Anderson method.
I have estimated that the plane should not weight more than 700 kg (according to the equations) to still be able to take off and climb with single engine. This may be too optimistic figure, I have been thinking that the limit might be rather near 650 kg or maybe even a bit less.
Thinking pessimistic: the plane can have positive climb rate with 60 hp single engine mode if the gross weight is 600 kg. That gives:
600 - 55 kg - 10 kg - 55 kg - 10 kg = 470 kg for the airframe + useful load excluding engines.
For useful load, minimally needed is:
- Two big adults, 95 kg including heavy clothes per each
- 5 kg baggage per each
- 120 liters of gasoline = 85 kg
This becomes:
95 kg * 2 + 10 kg + 85 kg = 285 kg.
For the plane to be minimally useful, it must be able to carry 285 kg in addition to its own weight. There are two engines and to have useful endurance the amount of fuel has to be double the size of a single engine plane.
The airframe + systems maximum weight excluding engines then becomes:
470 kg -285 kg = 185 kg
This means that the airframe + systems excluding engine can only weight 185 kg. This is a very hard goal to achieve.
The aircraft empty weight then becomes:
185 kg + 65 kg + 65 kg = 315 kg
The empty weight to gross weight ratio becomes:
315 kg / 600 kg = 0.52
This ratio is very challenging to achieve for a twin where the airframe must be carrying in addition to the occupants instead of one engine, two engines, and their fuel.
If we could still take off at 650 kg, then this becomes:
Airframe weight can be increased with 50 kg: 185 kg + 50 kg = 235 kg
235 kg + 65 kg + 65 kg = 365 kg
Looks like now we are talkin. This looks like a figure which might be theoretically possible, even though this is still very hard goal. As seen on ultralight planes, achieving empty weight under 300 kg is very hard. Adding extra engine on top that requires aircraft that is as lightweight than best ultralights equipped, plus can still take the additional engine.
But this is just theoretical thinking and whether or not it may be feasible, the discussion can continue:
The empty weight to gross weight ratio then becomes:
365 kg / 650 kg = 0.56
Historical data shows that at least on a bit larger aircraft, the 0.56 value is pretty well achievable.
Lets consider now the performance for the 650 kg case:
Single engine produces only 60 hp power. Only the excess power can be used for climb. This means that in a side slip of asymmetric thrust and climb angle of attack, the total drag (drag due to lift + fuselage drag) must be less than the thrust of 60 hp at best climb speed with a propeller that has efficiency of 0.7 (for pessimistic evaluation, I prefer to not use 0.85) by a large margin, and then the climb rate pretty much becomes from the weight to be lifted and how much excess power is still left.
The power loading for single case would be: 23.8 lbs/hp. This would be about the same as Diamond DA42. The drag must be low in order to ensure that the power needed for level flight is small, and there is excess power for climb, even with very low power.
Then comes the disaster of increasing wing area, this increases drag, but on the other hand, increases also lift. However, to get good cruise performance on the low power, wing size should be as small as possible. So some compromise is needed here. Increase in wing loading has to be accounted with increase in aspect ratio to keep the induced drag the same. Increase of aspect ratio may increase weight, but does not necessarily always do so. For example the earlier mentioned LH10 has very light wings, despite of aspect ratio of 14. So it worths researching on this area. A good design is a synergetic design which combines couple of good things into one good compromise.
I maybe need to redo the calculation yet another time again.
Why I am thinking this?
- For a plane that I would design for myself, I could choose Rotax 912ULS, and get two used engines with about half the price of a new Rotax 912ULS. This would be roughly the cost of a pair of new HKS700E.
- However, if we think a kit-builder who wants to have a twin with shoestring budget. Many aviators are limited with budget (aviators are always rich simply does not seem to be true, and if they originally were, they no longer are after starting spending to flying). So we have been thinking of a concept of a light plane with two engines with good performance. Any twin out there, even used ones, cost many many times more than it would cost to build a plastic one with two little HKS700E engines.
- I think that twin engine aircraft are not so popular, not because they require the additional license, but because people do not opt for the additional license, because the cost of the twin is prohibitive. There is absolutely no twin out there where one could log twin engine time and which would not cost a fortune of a millionaire to own or cost a fortune of of a normal people to maintain and operate.
- It is often explained that twins are more dangerous than singles. However, the context seems to be forgotten. Single engine limits the use of the plane and with two engines, people may often go to more dangerous situations.
- And it is not only a bad thing, consider this: You live in Finland and want to visit for example Greenland. What do you do if you want to fly there by yourself and not to sit as a passenger on an Airbus? You go and start your C172 and head towards Greenland. If the one old-fashioned engine that is almost approaching car engines in reliability, that is there, quits, then you are in biiig trouble. Wouldn't it be great if there was a second engine and you could still fly even if the one failed. Even if the climb rate with single engine is poor, you could still maybe get out of there alive. Your speed would get slow, but also your fuel consumption becomes half because only one engine is drinking the fuel. You actually might make it and your relatives don't need to arrange funerals.
Any comments on this?
Tuesday, January 20, 2009
Boom tail microlight/LSA
I was thinking which could be a suitable configuration if target would be to the microlight category (Finnish ultralight will be aligned with European microlight), or to EASA LSA category. The US-LSA category is stupid since it has some severe limitations which removes the reason to try to optimize anything - the speed limitation and also the stall speed limitation as clean -> with these limitations, it does not worth optimizing the aerodynamic performance or flap configuration, for US-LSA, the best solution probably would to design a plane, which is as lightweight as possible and which would not have any kind of flaps and which would achieve the stall speed only with the wing area (because that is what the limitation implies anyhow), so the utilized Clmax becomes close to 1.0, which is poor.
The main criteria in this more sane European category is the weight and the second main criteria is the stall speed. These are the most important features, other features are secondary. The performance can not be optimal, but it can be optimized to the constraints given by the weight and stall speed limitations. It would be also necessary to cut the part count to minimum, an inexpensive plane will be for sure more popular than the more expensive one, in the category where the buyers are not the richest people out there (who would anyhow order a Cirrus-Jet), but normal hobbyists who are not swimming in money.
So consider this:
- Plane structure would be based on carbon fiber rods (pultrusion rods).
- The fuselage would not be a structural member of the plane, but rather a baggage pod located below the spars. The twin booms would be a pultrusion rod each. The engine would be mounted to the wing spar rather than to the fuselage. These rods could have aerodynamic fairings on top of them (which also allow space for control cables etc.).
- high aspect ratio wing, which enables good climb rate with low power
- HKS700E engine in pusher configuration
- Fixed pitch pusher propeller behind the pod (but thrust line to the wing spar).
- inverted V-tail in the ends of the two booms, and the tail would connect the
two booms with the help of a pultrusion rod which functions as spar.
- Main landing gear connected to wing spar
- Nose gear located under the pod.
- Wing structure would be solid blue styrofoam, and in wing root there would be a large fairing which contains fuel (on both sides). The wing skin could be either carbon fiber or fiberglass (fiberglass to reduce cost obviously)
Think how many parts this requires compared to how many parts and layup schedules is usually needed. The pod type cockpit could be almost a complete monococue. There would be need for only instrument panel and some structure where one can assemble the pedals. Also the instrument panel, as we know it, does not need to be like it is, a panel. There are other ways arranging instruments in the plane than having a straight panel where everything is put with tiny screws. None of the modern cars use that old-fashioned way anymore. With modern avionics, you don't need a big panel with lots of switches, knobs, circular gauges etc. You can have just two screens which display and control everything.
The only strength needed in the fuselage is for crashworthiness, it does not need to carry any loads, and it does not need to be shaped unoptimally to avoid flutter tendency for example, all structural members are straight lines and separate from the fuselage.
The idea comes from some NASA PAV concepts, but as modified. It also has some influences from the Sunseeker.
The concept could have idea of being as lightweight as possible (the lower power engine also supports this mission) and still being as highly performing as possible (that can be achieved with the light weight and aerodynamics, not so much trust is needed).
So the performance target setting for conceptual design could be:
- beat 100 hp Dynaero MCR-ULC in empty weight with large margin
- be on par with 100 hp Dynaero MCR-ULC in speed (with only 60% of the power available)
- and the rest comes from the category limitations
- be a lot cheaper than most other same category plane on the market
- climb rate 800 fpm (remember that because of the low climb speed, the climb gradient is high despite of the not so high number compared to high performance aircraft)
Compromise:
- beat 100 hp Dynaero MCR-ULC in empty weight
- cruise speed compromised to between 80 hp WT9 Dynamic and 80 hp MCR.
- climb rate 600 fpm
Failure:
- heavier than MCR-ULC
- slower than 100 kts in cruise
- climb rate less than 500 fpm
Anyone interested in a such thing or having ideas (for or against) for a such thing?
Here is an illustration about the idea (15 minutes of Rhino magic):
The main criteria in this more sane European category is the weight and the second main criteria is the stall speed. These are the most important features, other features are secondary. The performance can not be optimal, but it can be optimized to the constraints given by the weight and stall speed limitations. It would be also necessary to cut the part count to minimum, an inexpensive plane will be for sure more popular than the more expensive one, in the category where the buyers are not the richest people out there (who would anyhow order a Cirrus-Jet), but normal hobbyists who are not swimming in money.
So consider this:
- Plane structure would be based on carbon fiber rods (pultrusion rods).
- The fuselage would not be a structural member of the plane, but rather a baggage pod located below the spars. The twin booms would be a pultrusion rod each. The engine would be mounted to the wing spar rather than to the fuselage. These rods could have aerodynamic fairings on top of them (which also allow space for control cables etc.).
- high aspect ratio wing, which enables good climb rate with low power
- HKS700E engine in pusher configuration
- Fixed pitch pusher propeller behind the pod (but thrust line to the wing spar).
- inverted V-tail in the ends of the two booms, and the tail would connect the
two booms with the help of a pultrusion rod which functions as spar.
- Main landing gear connected to wing spar
- Nose gear located under the pod.
- Wing structure would be solid blue styrofoam, and in wing root there would be a large fairing which contains fuel (on both sides). The wing skin could be either carbon fiber or fiberglass (fiberglass to reduce cost obviously)
Think how many parts this requires compared to how many parts and layup schedules is usually needed. The pod type cockpit could be almost a complete monococue. There would be need for only instrument panel and some structure where one can assemble the pedals. Also the instrument panel, as we know it, does not need to be like it is, a panel. There are other ways arranging instruments in the plane than having a straight panel where everything is put with tiny screws. None of the modern cars use that old-fashioned way anymore. With modern avionics, you don't need a big panel with lots of switches, knobs, circular gauges etc. You can have just two screens which display and control everything.
The only strength needed in the fuselage is for crashworthiness, it does not need to carry any loads, and it does not need to be shaped unoptimally to avoid flutter tendency for example, all structural members are straight lines and separate from the fuselage.
The idea comes from some NASA PAV concepts, but as modified. It also has some influences from the Sunseeker.
The concept could have idea of being as lightweight as possible (the lower power engine also supports this mission) and still being as highly performing as possible (that can be achieved with the light weight and aerodynamics, not so much trust is needed).
So the performance target setting for conceptual design could be:
- beat 100 hp Dynaero MCR-ULC in empty weight with large margin
- be on par with 100 hp Dynaero MCR-ULC in speed (with only 60% of the power available)
- and the rest comes from the category limitations
- be a lot cheaper than most other same category plane on the market
- climb rate 800 fpm (remember that because of the low climb speed, the climb gradient is high despite of the not so high number compared to high performance aircraft)
Compromise:
- beat 100 hp Dynaero MCR-ULC in empty weight
- cruise speed compromised to between 80 hp WT9 Dynamic and 80 hp MCR.
- climb rate 600 fpm
Failure:
- heavier than MCR-ULC
- slower than 100 kts in cruise
- climb rate less than 500 fpm
Anyone interested in a such thing or having ideas (for or against) for a such thing?
Here is an illustration about the idea (15 minutes of Rhino magic):

Labels:
aircraft concept,
idea,
LSA,
microlight,
ultralight
Subscribe to:
Posts (Atom)